Various ancient cultures figured out how to dye fibers indigoid blue, yet it was only in India that indigo pigment was extracted, concentrated, and dried into lightweight blocks. These could be stored indefinitely, transported across continents, and rehydrated as needed.1 This was a major advantage in dealing with dyes that came from bulky dyestuffs, large quantities of which were needed to obtain deep shades.2 As early as the Indus Valley Civilization (3300–1300 BCE), Indian artisans mastered four scientific principles of indigo dye. They understood the botanical advantages of the Indigofera genus; the chemistry of extracting blue pigment from such plants; the biochemistry involved in converting the pigment to a soluble color- and wash-fast dye; and the physics of the perception of color. The capacity to manufacture not only pigments but also textiles patterned in indigo in large quantities, commoditize, and trade them earned India its name.3 Through enterprise, expertise, and artistry, Indian textiles dominated the global trade until the industrial revolution of the nineteenth century. Of these textiles, hand-painted chintz became the most popular type traded west and east of the subcontinent. Peninsular India produced indigo pigment and developed its own rich traditions of dyed, resist-dyed, painted, and block-printed textiles. The southeastern Coromandel Coast was a well-known center where the Dutch commissioned blue-on-white chintz.
Against this backdrop of Indian savoir-faire, the present essay highlights indigo in South India with several vignettes. These range from a palm leaf manuscript from Kerala dated to 1818 that mentions indigo cultivation to a traditional South Indian indigo vat recipe that was passed on by Katubadi Yellappa, one of the few master dyers left in the 1960s, and to his disciples, who continue to keep this practice alive. Another set of vignettes examines the use of indigo in three fragments of chintz from the Cotsen Textile Traces Study Center at The George Washington University Museum and The Textile Museum. The essay also discusses indigo-dyed textiles that were made for domestic consumption and that are now being produced on a small scale by sustainable social enterprises.
Of the 60 Indigofera species found in India, the plants that yield the highest percentage of pure pigment are I. tinctoria L., I. sumatrana Gaertn., I. disperma L., and I. argentea.4 These plants and the techniques developed to extract, dehydrate, and stockpile pigment are at the heart of India’s domination of the global textile trade.
First, harvested indigo-bearing leaves ferment in large water tanks. Indican, a substance from the leaves, transfers to the aqueous solution, which is vigorously mixed to introduce oxygen. As the indican combines with oxygen, it turns into insoluble blue crystals that sediment in water. This sedimented pigment is dried, formed into cakes, and stored. Quality indigo is light, porous, and readily broken and ground into a powder. It is highly concentrated, so only small quantities are required to richly color fiber.
In South India, the states of Tamil Nadu, Andhra Pradesh, and Telengana have historically been centers for indigo production. To date, organic indigo is cultivated and processed in Tamil Nadu by Dada Enterprises, established around 1835 on about 300 acres. KMA (Kongarapattu Manickam Anbalagan) Exports, a similar enterprise, produces around 5,000 metric tons per year. Surprisingly, a palm leaf document dated to 1818 reveals that indigo was also cultivated at Kolachel, which was then part of Kerala (Figure 1). As there was much demand for indigo there, the ruler granted tax relief for three years to an indigo farmer named Mesther Virutheru Beck. When Beck passed away, the farmers who succeeded him were granted a second three-year period of tax relief.
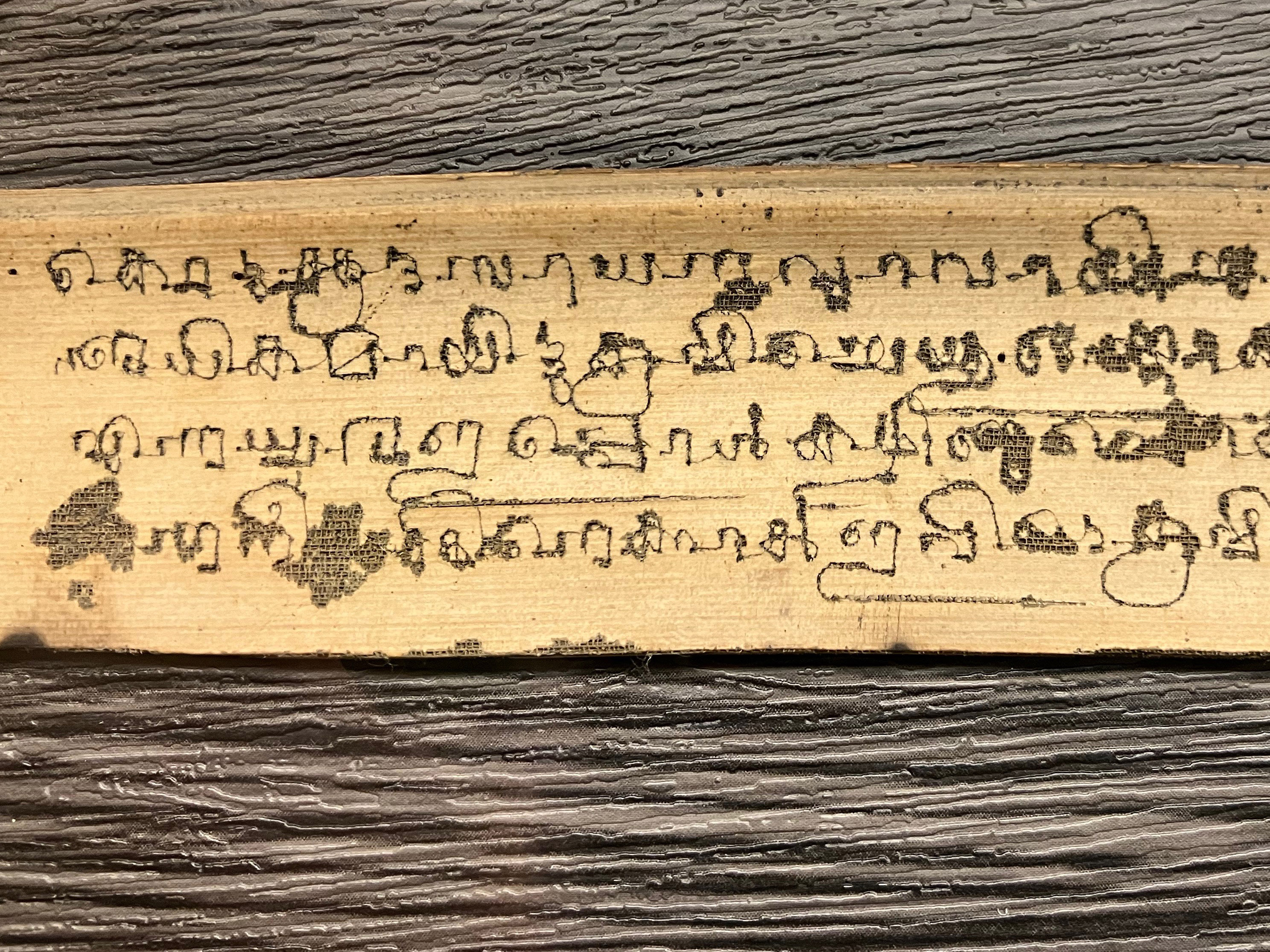
Indigo molecules must be broken apart for the pigment to be soluble. Powdered pigment is dissolved in a vat, breaking the bond between oxygen and indigotin temporarily (a process known as reduction) to create a soluble form of the dye (known as indoxyl). When fibers are soaked in the indoxyl, the indoxyl molecules penetrate the surface. Then, when the fibers are exposed to air outside the vat, oxygen combines with the indoxyl to form insoluble indigo molecules once again. The dye is trapped in the fiber, and this is the blue we see. Color is not deepened by soaking the fiber for longer periods. Instead, color is built up. Each dip in the vat, followed by exposure to air to oxidize the indigo molecules, increases the depth of the blue pigment deposited on the fiber. This is true of other dyes as well, but dip-dyeing with indigo is a controlled process.
Reduction, or splitting oxygen from indigo molecules, can be achieved either via slow fermentation, done by bacteria, or more quickly, with minerals and chemicals. Bacterial indigo reduction is more environmentally friendly. In India, however, resuming the practice of producing dye in a sustainable way has yet to be taken seriously by the government or the scientific community.5 In Japan, since the government declared the traditional indigo-dyeing process an important intangible cultural heritage, scientific studies to understand and improve natural indigo dyeing have been encouraged.6 It is now known that a range of bacteria evolve in indigo vats, and the behaviors and requirements in terms of temperature and pH differ for each of them.7
Traditional Indian recipes for indigo vats vary according to regional resources. They all reflect a basic understanding of the biochemical process of indigo fermentation. By combining indigo pigment with a saccharide (a reducing agent) and tepid alkaline water, environments for naturally occurring microbial communities are created. Master dyers use their sense of smell and, sometimes, taste while monitoring and stirring their vats up to three times a day. A dark-blue foam or “flower” on the surface of a vat is taken as proof of a healthy vat. The flower occurs when the reduced indoxyl on the surface of the vat combines with oxygen in the open air to form insoluble blue indigo molecules.
This care given to vats helps thermophilic, alkaliphilic, and anaerobic microbiota proliferate and renew continuously.8 When these bacteria are able to feed on complex sugars and the oxygen in the indigo molecules, molecules of indigo are reduced for optimal dyeing. No two vats behave in the same way, and the bacteria can take anywhere from three to ten days to start absorbing the oxygen in the indigo molecules. The dyeing process causes instability for the microbiota in the vat, as outside microbes are inevitably introduced while dipping fibers.9 If the vat is left undisturbed, neutrophilic bacteria (those that survive in a neutral pH environment) proliferate and destroy the beneficial indigo-reducing bacteria.10 This explains why each vat is carefully stirred and nurtured daily.
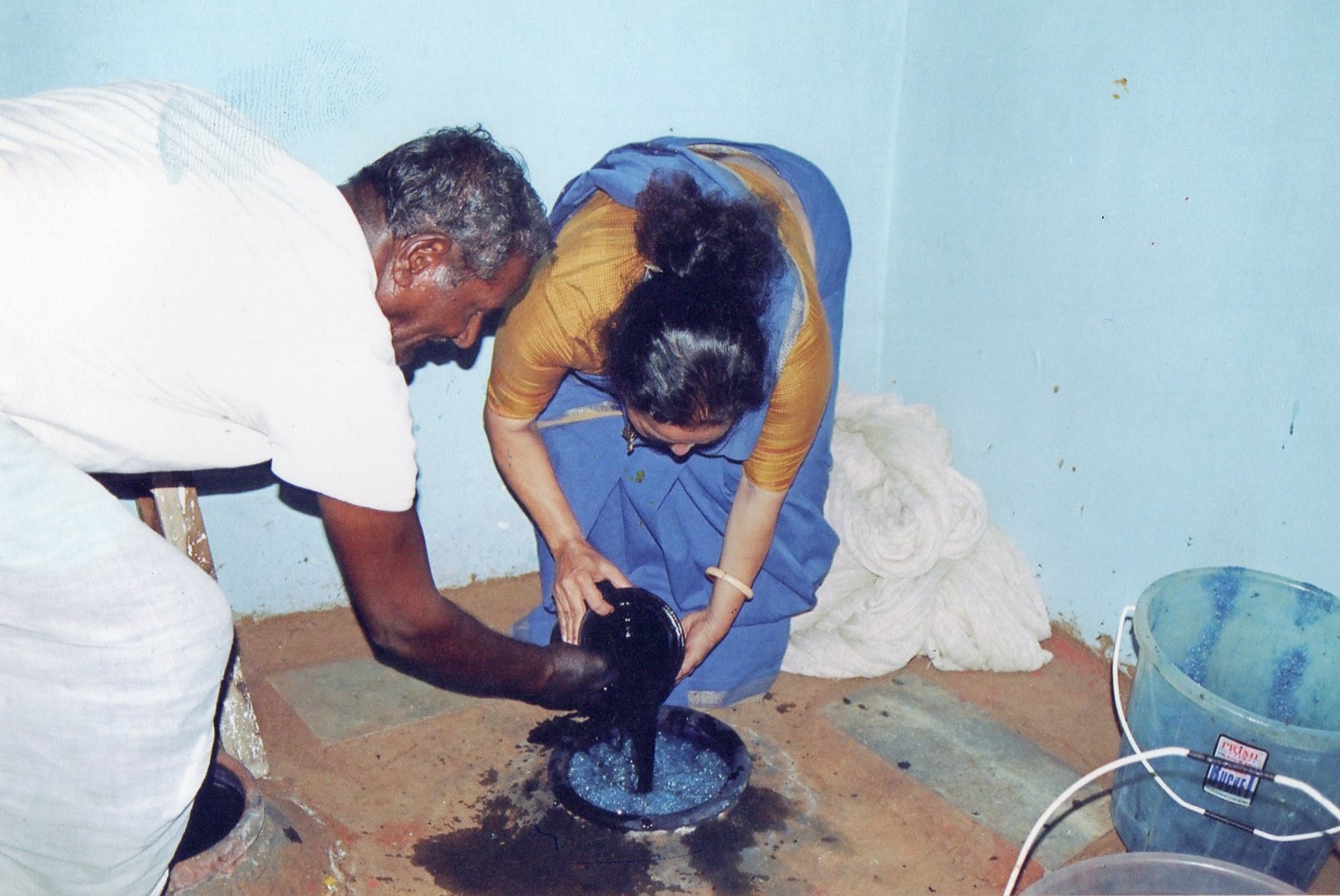
Indigo artisans fiercely guarded their recipes. Moreover, the traditional method of setting up the vat, nurturing it, and dyeing with natural indigo requires deep commitment, and master dyers could be skeptical of novices. Luckily, Yellappa, one of the last master dyers, transmitted his knowledge to his disciples Jagada Rajappa and Odhellu, who teach and keep his recipe alive (Figure 2).11
1 lb., 10 oz. (750g) dry indigo cakes
40 gallons (150L) water
2 lb., 3 oz. (1.5kg) Cassia tora seeds
2/3 to 1 1/3 cups (100 to 200ml) water, filtered through a mixture of two portions of Saulu-matti (earth rich in sodium carbonate) and one portion of ash
Slaked lime (calcium hydroxide) in increments of 3 1/2 oz. (100g)
Day 1
Grind the indigo cakes with enough water to make a smooth paste. Allow to hydrate overnight. Place Saulu-matti and ash in a pot with a hole at the bottom. Pour water on top, and let the alkali water filter into a receptacle.
Day 2
Boil Cassia tora seeds for approximately 3 hours over a slow fire until soft and glistening. In an earthen vat, combine indigo paste, water, cooked C. tora, and alkali water. Stir with a wooden dowel.
Days 3 to 5
Stir thrice a day, adding slaked lime gradually. The pH must come to twelve. Skim off Cassia tora seeds that float to the surface. The vat is ready for dyeing when it smells a bit like the ripe fruit of durian.
Once an organic indigo vat has been established, it is usually maintained for three years, and its ingredients are replenished every six months. Having a dye vat that can be used repeatedly is a bonus, and a typical workshop has forty to eighty vats. Dyeing is done by rotating among four vats, to allow the vats to regenerate in between dips.12
An indigo workshop has a raised platform with deep terracotta jars (vats) about 12 inches (30 cm) wide and 2 feet 3 inches (70 cm) high, embedded in goat or sheep dung up to their rims. Although goat dung is rich in nitrogen and bacteria, it cannot be composted alone, due to its low carbon-to-nitrogen ratio and a low amount of free air space, so it most likely provides insulation rather than heat.13 This keeps the temperature of the liquid in the indigo vat stable at about 86°F (30°C), despite the tropical weather experienced in most of South India. Once the dung has been tamped down around the pots, the surface around the rims is plastered over with a mix of cow dung and clay, as in the floors and walls of most village homes. This not only provides a level area of about two feet between the jars for the dyers to squat on while dyeing but also seals the goat dung, preventing it from composting too quickly.14
With a team of three workers, Jagada and her disciple Salim provided indigo-dyed yarn to handloom weavers working with Malkha, a social enterprise seeking to promote small-scale cotton farming, spinning, and weaving (Figures 3.1-3.2). Unfortunately, Salim met with a tragic accident soon after the author visited him and the workshop, and its activities went into disarray. Today, Odhellu, another disciple of Yellappa, has taken up the torch, training and helping Malkha with dyed indigo yarn (Figures 4–6). Jagada continues to train artisans in India and abroad.
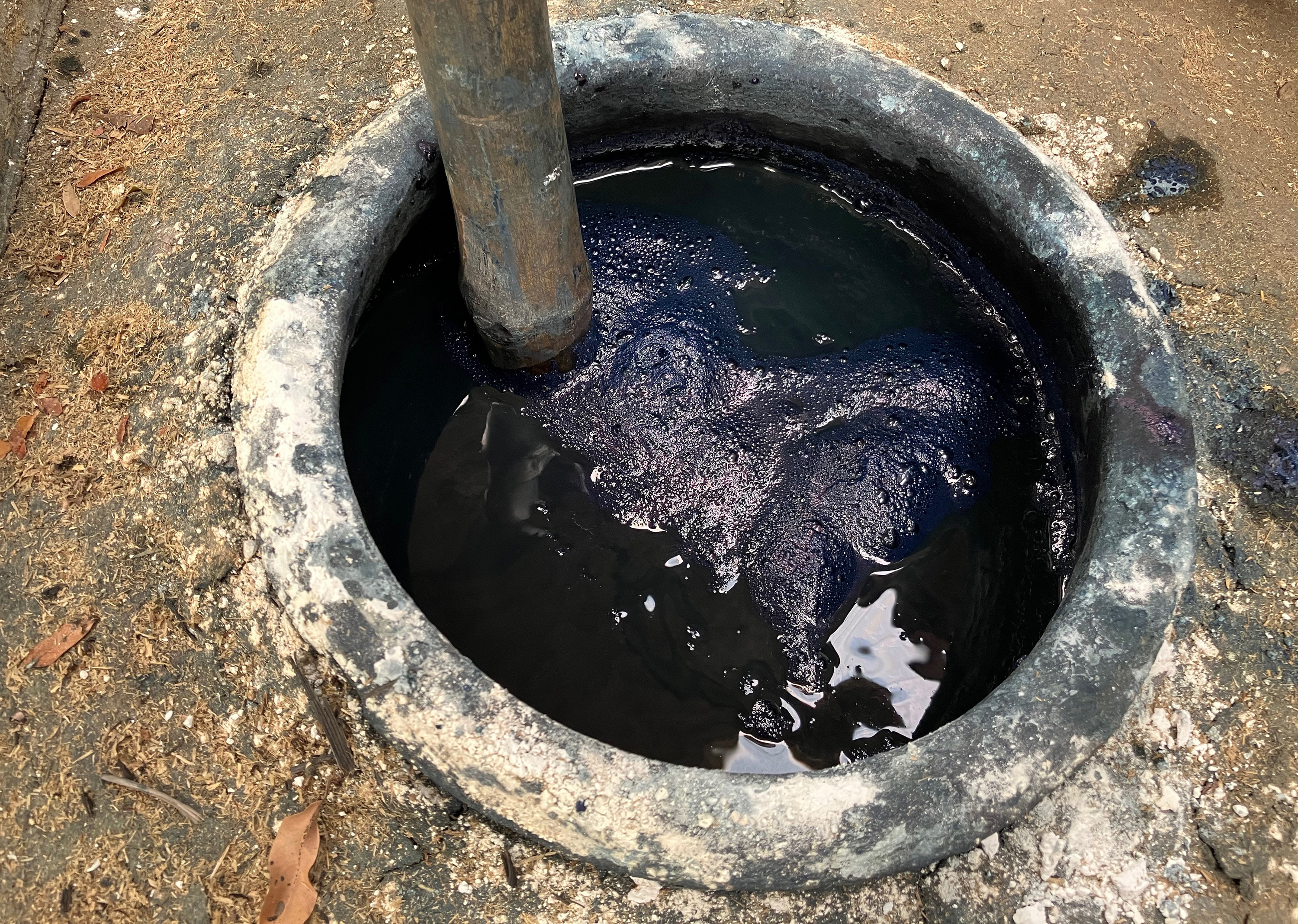
Indigo has several properties that textile makers in India used to their advantage. The alkaline indigo vat is ideal for cellulosic fibers such as cotton—notoriously difficult to dye and abundant in India.15 By controlling the pH of alkaline vats, they also dyed delicate protein fibers such as cashmere and silk.16 Indigo is a cold dye and therefore a good fit for resist dyeing. In South India, yarn-dyed plain weaves, single and double ikats, tie dye (Madurai Chungudi), and hand-painted and/or block-printed (Kalamkari) textiles were worn by both genders and continue to be produced for the domestic market.
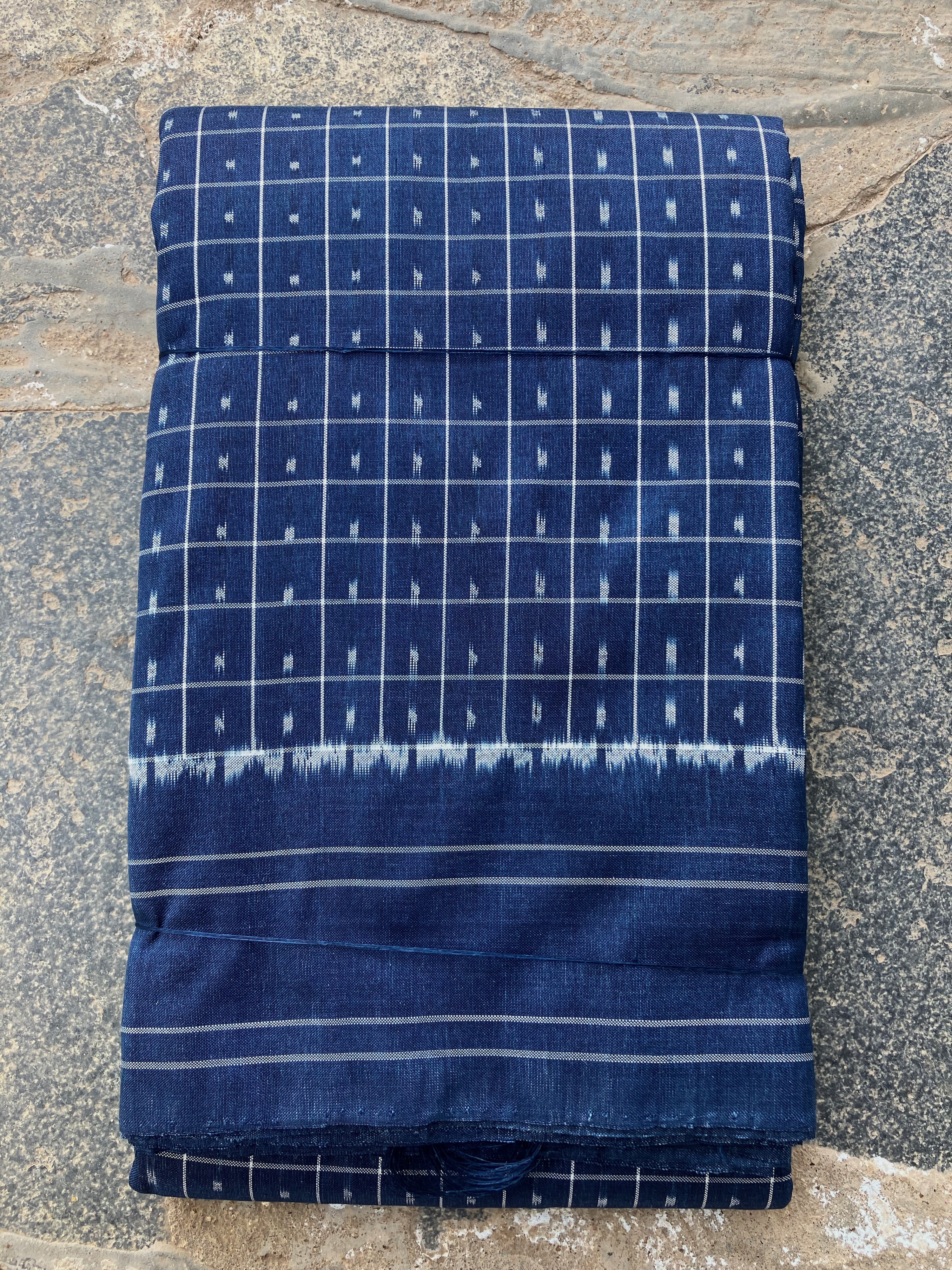
Dudyala Shankar, an ikat weaver in Koyyalagudem, Andhra Pradesh, creates limited-edition silk saris in indigo and other natural dyes (Figures 7–8).
With their deep knowledge of indigo and madder, Indian artisans played with permutations and combinations of techniques. They excelled at manipulating blue and red dyes to achieve multiple hues by dipping, resisting, overdyeing, and mordanting.17 By altering the number of dips, they created gradations of blue. By juxtaposing shades of blue with white or red, they achieved visual variations of color. By overdyeing blue with yellow, red, or black, they obtained greens, purples, and deep blue/black respectively.
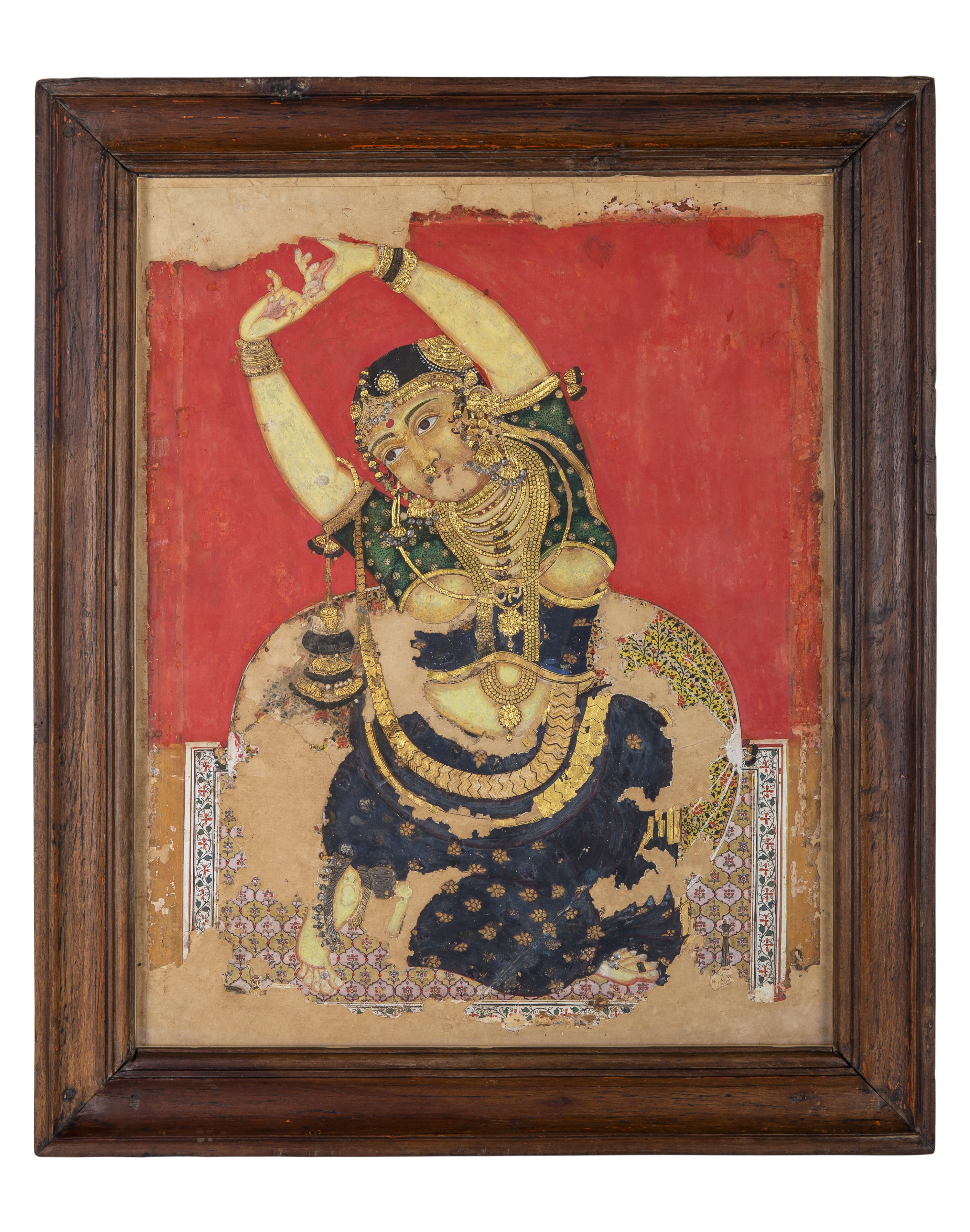
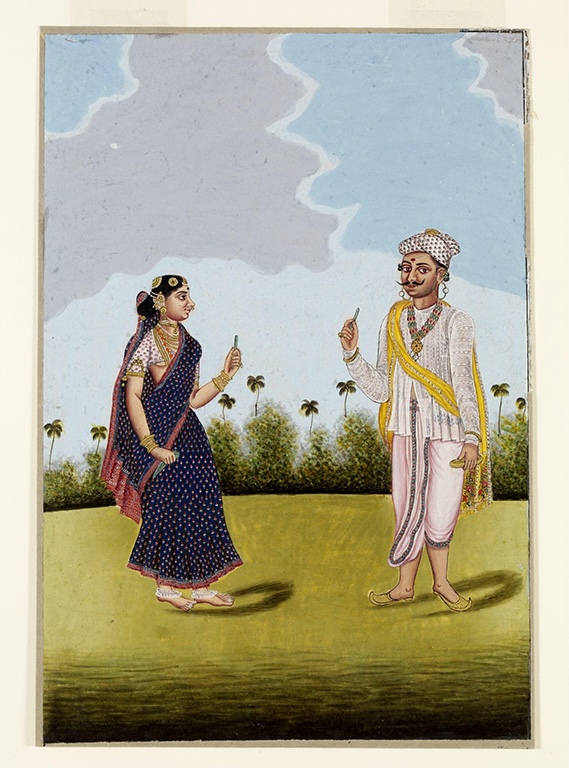
Blue was a favored color in traditional textiles in South India. It was often contrasted with other colors. We see men and women depicted in blue attire in the Tanjavur school of paintings (Figure 9.1) and so-called Company paintings made by Indian artists for the British in the 1800s. (Figures 9.1–9.3).
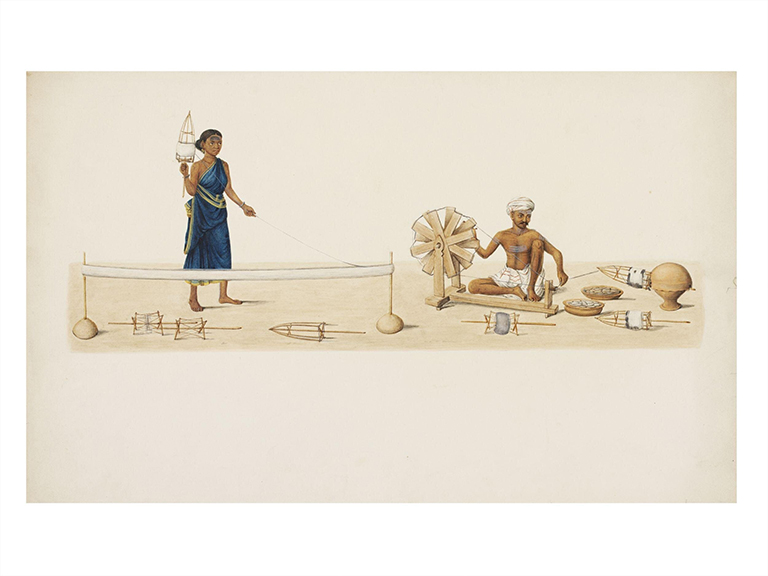
Both Malkha and Blue Lotus, a nonprofit organization that works with artisans in Andhra Pradesh promote the use of products in natural dyed fabrics. At Aranya Natural, a social enterprise in the Tata tea gardens of Munnar in Kerala, indigo along with other natural dyes is used to create slow fashion as a unique selling point for textiles made by differently abled adults. Such practices aim to be environmentally safe, with low carbon footprints, and they involve ethical artisanal production and slow fashion (Figures 10-11.2).

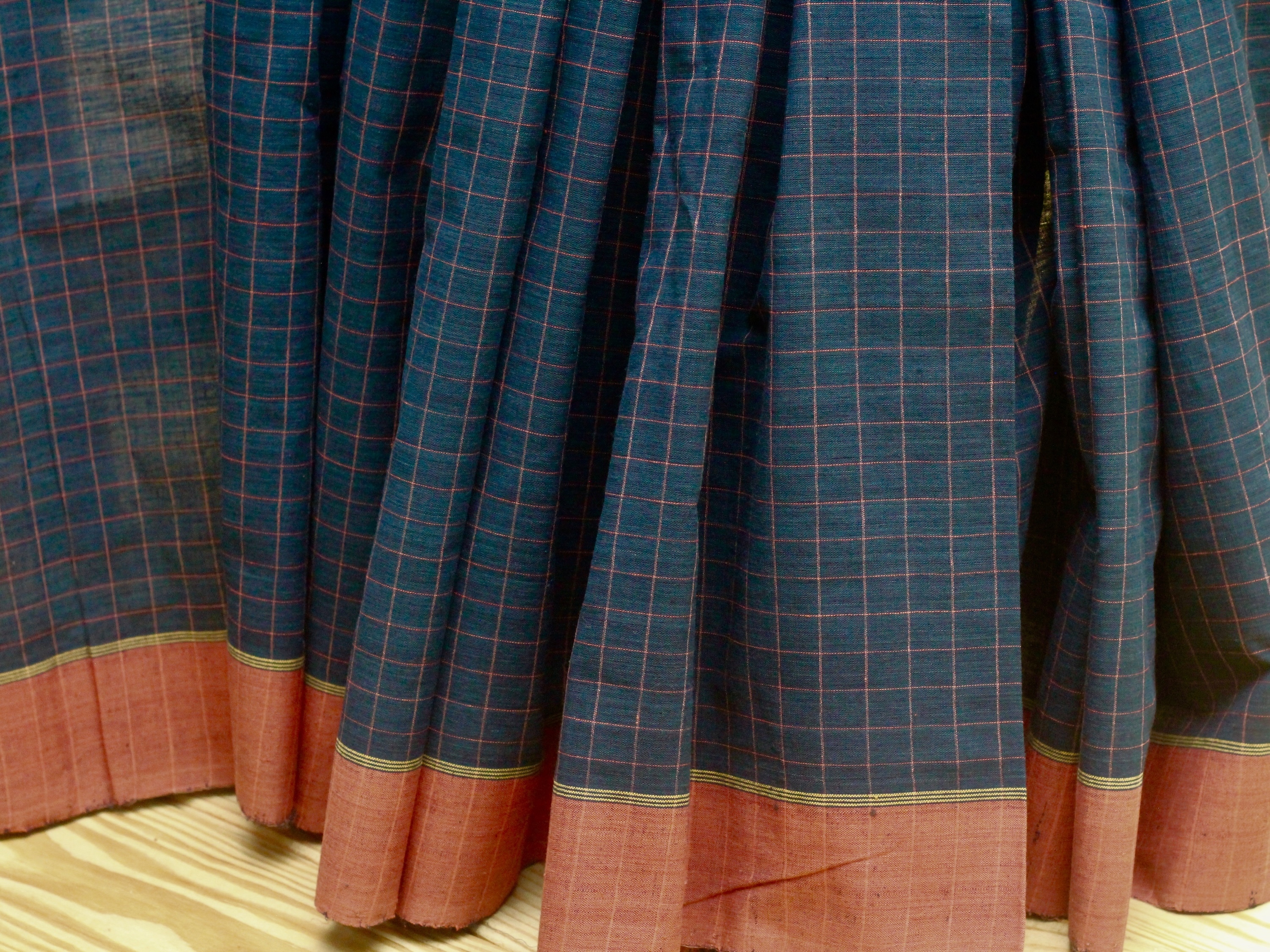
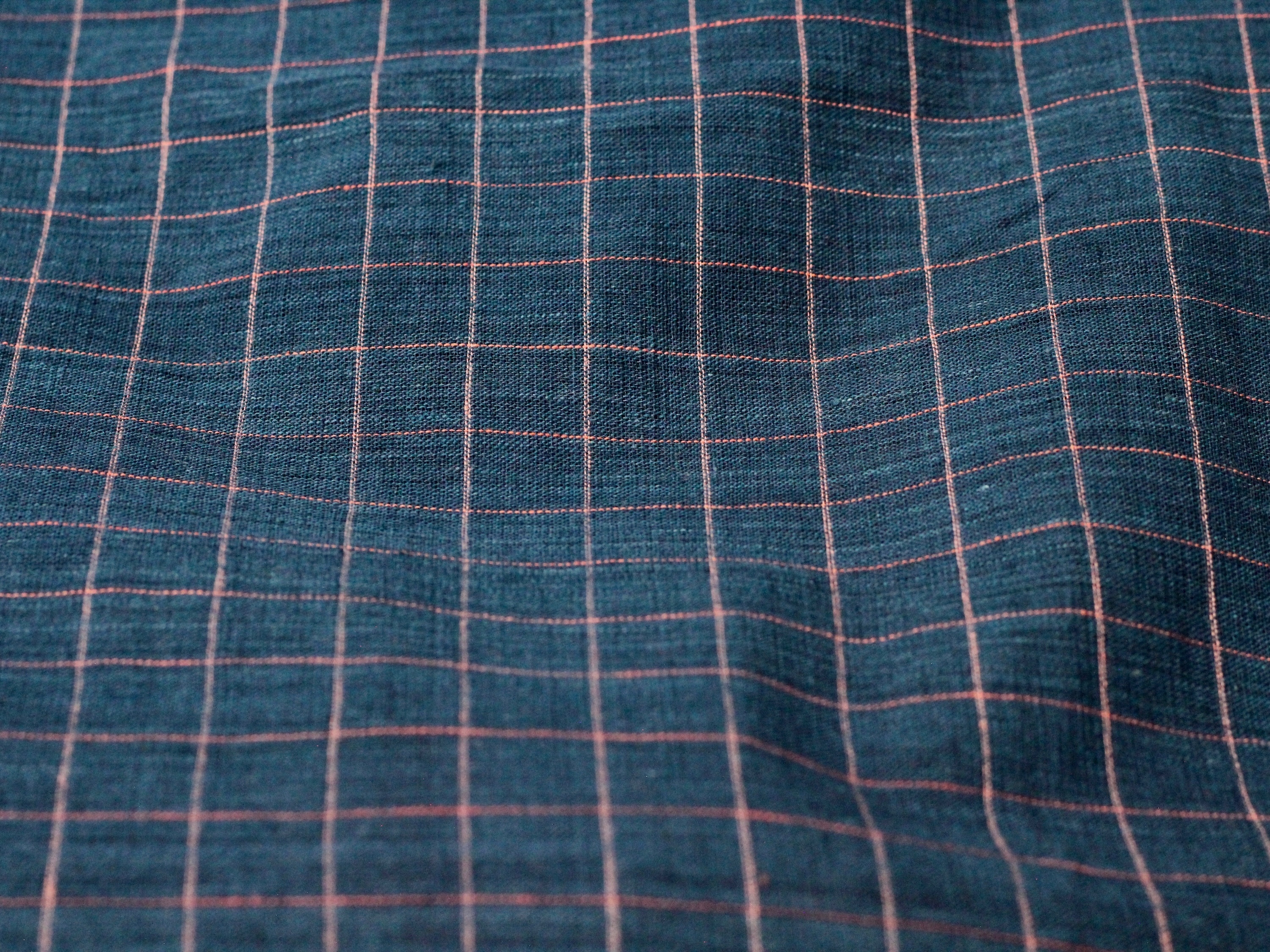
By the end of the fifteenth century, Europeans began trading Indian textiles with Southeast Asia for spices. When these textiles made their way to Europe, the local populations there were charmed by exotic patterns that were both vivid and colorfast, on comfortable, washable cotton. Through the artisans’ mastery of natural dyes and their adaptability to produce designs to suit the tastes of a wide audience emerged one of the world’s most popular textiles—chintz. Hand-painted chintz became world renowned, due to its range of spontaneous, colorful, eclectic designs. Varied colors and values were achieved with relatively few dyes—principally red and blue—and the use of stippling textures, lines, and dots. These textiles were extremely influential in Europe, sparking the curiosity of many dyers and textile manufacturers, resulting in a transfer of techniques that changed the face of global trade and capitalism.
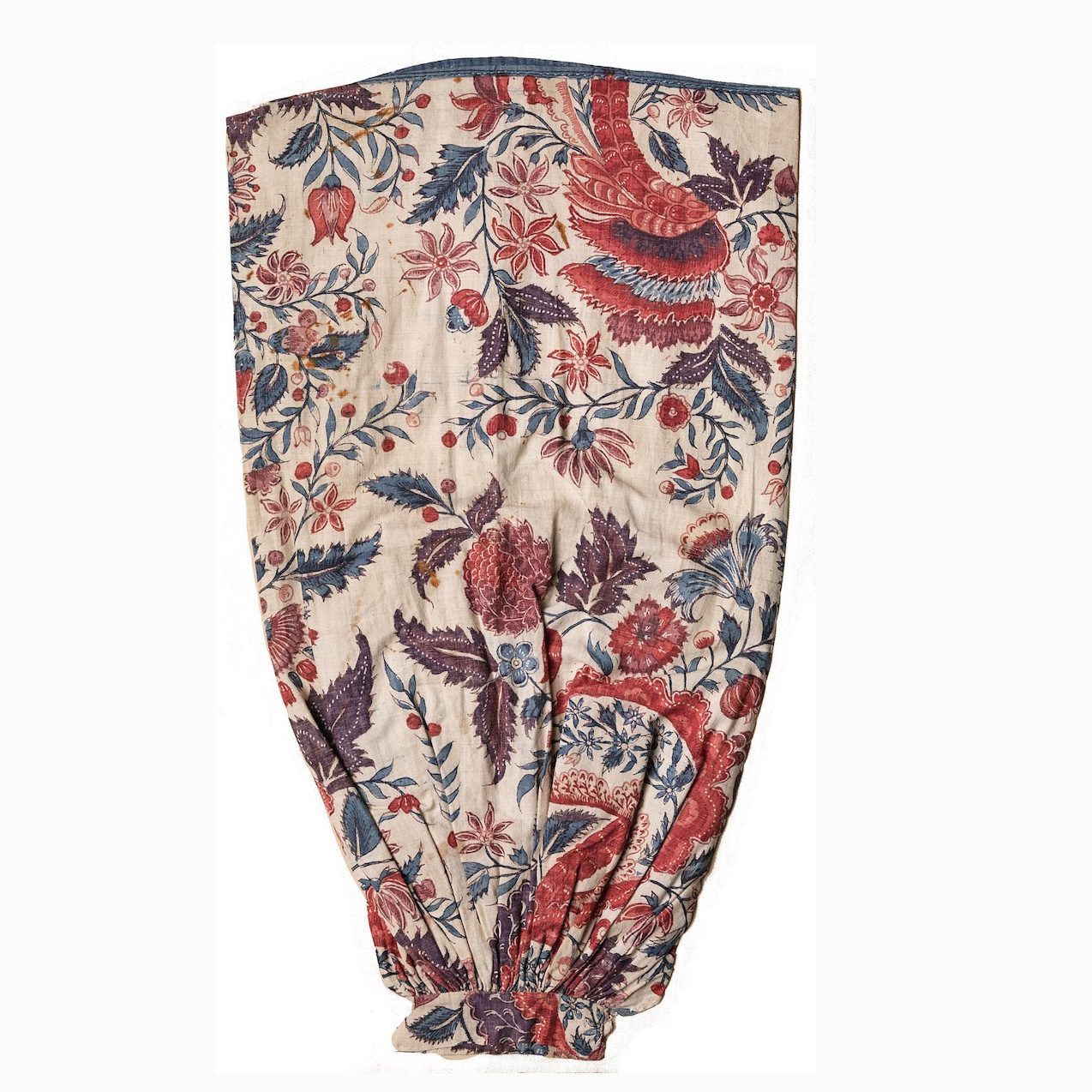
Chintzes from the Coromandel Coast tend to have various shades
of red and blue as their principal colors, unlike in North
India, where green was favored over blue.18
The Cotsen Textile Traces Study Collection T-2496’s typical
floral pattern appears to be multicolored due to the use of
different mordants to achieve shades of red and purple,
contrasted with blue. By dipping the textile in indigo a
minimum number of times, a medium blue was created. Despite
such careful restraint, close inspection reveals barely
visible fine vertical lines where the protective resist paste
may have cracked, and the indigo dye seeped onto the white
background. Clever overprinting on the blue with black and
purple adds to the illusion of multiple shades of blue. The
spontaneous lines, fine brushwork for textures in the
fantastical flora, and movement in the pattern contribute to
the rich and dynamic floral pattern (Figure 12).

Another type of chintz that found favor with the Dutch, both in Europe and among Dutch immigrants in North America was the single-color pattern on a white background—red-on-white, black-on-white, or blue-on-white. This type was the most complicated to achieve, as the entire white background had to be painted with a resist. Unlike in Indonesian batik, where cracks in the resist are favored or at least accepted, blue-and-white chintz was meant to have as white and “clean” a background as possible. One such fragment has a finely drawn floral pattern in a dark shade of blue, with some areas that appear blue/black on a white background. Small dots and short lines within the floral pattern are typical of a flowing resist like hot wax. The background is remarkable for its pristine white. The blue/black areas were achieved by overpainting an iron-based, deep brown dye (Figure 13).

Much has been written about the tumultuous history of North Indian indigo, but this critical industry was also encouraged by both precolonial and colonial powers in peninsular South India. Indian indigo, manufactured across the subcontinent, developed a reputation for high color yield and was an important aspect of the country’s market power. Indigo farmers and processors were given tax breaks, dried indigo pigment was exported from the coastal ports, and innovative textiles were created for both internal and external markets. Renewed interest in natural indigo pigment has encouraged farmers like Dada and KMA Exports.
To avoid uncertainty and quicken the process, many artisans now resort to synthetic indigo and quick-fix chemical reduction agents. These include sodium dithionite, also known as sodium hydrosulfite or Hydro, and thiourea dioxide, both of which are polluting and pose health hazards. In the context of today’s noxious, energy-intensive, and exploitative textile industry, there is a holistic opportunity to revisit traditional South Indian uses of indigo, not only as a dye but also as a medicinal plant and green manure. It is hoped that further scientific inquiry of natural indigo vats will help to bring sustainable solutions.
Chintz came about from global influences, and the expertise of natural indigo dyeing was a key element in its market share. Although we no longer see the chintz of yesteryear, today, small-scale production as practiced by Malkha, Aranya Natural, and Blue Lotus continue the traditions of hand-spinning endemic cotton, dyeing with natural indigo, and handweaving. Once again, global influences, markets, and traditions are coming together, with the potential to supply ethical clothing to the world.
I am grateful to Barbara Hanson Forsyth, Jagada Rajappa, Kavita Meegama (Brhat.in), Odhellu, Oorja Shettigari, Noupour and Pierre Audinet, Salim, Satish Poludas Nagendra, Swati Dandekar, Uzramma (Malkha), and Mr. and Mrs. Narayanan. I would also like to acknowledge Michel Garcia and Jonathan Mark Kenoyer, whose public talks helped me to understand the biochemistry and history of indigo. Special thanks: Dr. Maya B., Rahul Krishnan G., and Parvathi S. (Palm leaf manuscripts museum, Central Archives, Thiruvananthapuram, Kerala)
Notes
-
Indigo is the term for the color, the dye, or the pigment. Indigotin, the blue coloring compound of indigo dye, is the term used when we are not sure of the exact plant the dye was extracted from. The word indigoid refers to something that relates to or resembles indigo, especially in chemical structure or dyeing properties. The dye bath is the indigo vat. ↩︎
-
Natural dyes were mostly derived by crushing and boiling dyestuffs––either fresh or dried leaves, roots, flowers, bark, or fruit. ↩︎
-
As early as the first century CE, people in the Greco-Roman world believed that indigo came from India. ↩︎
-
B. C. Mohanty et al., Natural Dyeing Processes of India (Ahmedabad, India: Calico Museum of Textiles, Sarabhai Foundation, 1987). ↩︎
-
Although no focused studies on the bacteria in I. tinctoria dye vats were found at the time of writing this essay, a study on the antibacterial, antioxidant, and cytotoxicity effect of I. tinctoria on lung cancer cells revealed that the leaf extract inhibited the growth of certain bacteria, such as Staphylococcus aureus and Streptococcus pyogenes, while it did not do so for others such as Escherichia coli and Pseudomonas aeruginosa. See K. P. Renukadevi and S. Suhani Sultana, “Determination of Antibacterial, Antioxidant and Cytotoxicity Effect of Indigofera tinctoria on Lung Cancer Cell Line NCI-h69,” International Journal of Pharmacology 7, no. 3 (2011): 356–62. ↩︎
-
Research on the microbiota found in Japanese fermentation vats using Persicaria tinctoria plants have isolated several indigo-reducing bacteria, such as Bacillus alkaliphiles (discovered in 1960 by Takahara and Tanabe). ↩︎
-
One study found that the addition of dried Indigofera leaves ameliorated color yield in Japanese vats. ↩︎
-
Thermophilic refers to microorganisms that thrive at high temperatures; alkaliphilic refers to microorganisms that thrive in alkaline environments. Anaerobic microorganisms do not require molecular oxygen to survive. ↩︎
-
Tu Zhihao, “Analysis of the Changes in Microbiota Associated with Indigo Reduction in Natural Indigo Fermentation” (PhD diss., Hokkaido University, 2020), 1–2, https://eprints.lib.hokudai.ac.jp/dspace/bitstream/2115/80736/1/Tu_zhihao.pdf. ↩︎
-
Keiichi Aino et al., “Microbial Communities Associated with Indigo Fermentation That Thrive in Anaerobic Alkaline Environments,” Frontiers in Microbiology 9 (2018), doi: 10.3389/fmicb.2018.02196. ↩︎
-
Yellappa passed away in 2014. ↩︎
-
Mohanty et al., Natural Dyeing Processes of India, 91. ↩︎
-
Recep Kulcu and Osman Yaldiz, “Composting of Goat Manure and Wheat Straw Using Pine Cones as a Bulking Agent,” Bioresource Technology 98, no. 14 (2007): 2700–2704. The dung is said to release heat. No scientific research has shown that the dung generates heat over a period of several months. This aspect requires more research. ↩︎
-
B. C. Mohanty states that the jars are used for three years, after which they are renewed with new dung and jars; Mohanty et al., Natural Dyeing Processes of India, 91. ↩︎
-
Cellulosic fibers, taken from plants, include cotton, hemp, and linen. ↩︎
-
Protein-based fibers, taken from animals, include silk (secreted by insects), wool, and cashmere. ↩︎
-
Mordants are metal salts that are used to fix dyes on fiber, making them light and wash fast. When dyes do not bind naturally to fibers, mordants act as intermediaries that can bind both to the fibers and to the dyes. Mordants such as iron or alum can be used with the same dye to achieve different colors. ↩︎
-
Ebeltje Hartkamp-Jonxis, Sitsen uit India / Indian Chintzes (Amsterdam: Rijksmuseum, 1994), 28. ↩︎
Bibliography
- Aino 2018
- Aino, Keiichi, et al. “Microbial Communities Associated with Indigo Fermentation That Thrive in Anaerobic Alkaline Environments.” Frontiers in Microbiology 9 (2018), doi: 10.3389/fmicb.2018.02196.
- Balfour-Paul 1998
- Balfour-Paul, Jenny. Indigo. London: British Museum Press, 1998.
- Boutrup and Ellis 2019
- Boutrup, Joy, and Catharine Ellis, The Art and Science of Natural Dyes: Principles, Experiments and Results. Atglen, Pa.: Schiffer Crafts, 2019.
- Dandekar 2018
- Dandekar, Swati, director. Neeli Raag—True Blue. 85-minute documentary film, 2018.
- Hartkamp-Jonxis 1994
- Hartkamp-Jonxis, Ebeltje. Sitsen uit India / Indian Chintzes. Amsterdam: Rijksmuseum, 1994.
- Kulcu and Yaldiz 2007
- Kulcu, Recep, and Osman Yaldiz. “Composting of Goat Manure and Wheat Straw Using Pine Cones as a Bulking Agent.” Bioresource Technology 98, no. 14 (2007): 2700–2704.
- Mohanty, Chandramouli, and Naik 1987
- Mohanty, B. C., K. V. Chandramouli, and H. D. Naik. Natural Dyeing Processes of India. Ahmedabad, India: Calico Museum of Textiles, Sarabhai Foundation, 1987.
- Peck 2013
- Peck, Amelia, et al. Interwoven Globe: The Worldwide Textile Trade 1500–1800. New York: Metropolitan Museum of Art, New York, 2013.
- Renukadevi and Sultana 2011
- Renukadevi, K. P., and S. Suhani Sultana. “Determination of Antibacterial, Antioxidant and Cytotoxicity Effect of Indigofera tinctoria on Lung Cancer Cell Line NCI-h69.” International Journal of Pharmacology 7, no. 3 (2011): 356–62.
- Tu 2020
- Tu Zhihao. “Analysis of the Changes in Microbiota Associated with Indigo Reduction in Natural Indigo Fermentation.” PhD diss., Hokkaido University, 2020, https://eprints.lib.hokudai.ac.jp/dspace/bitstream/2115/80736/1/Tu_zhihao.pdf.